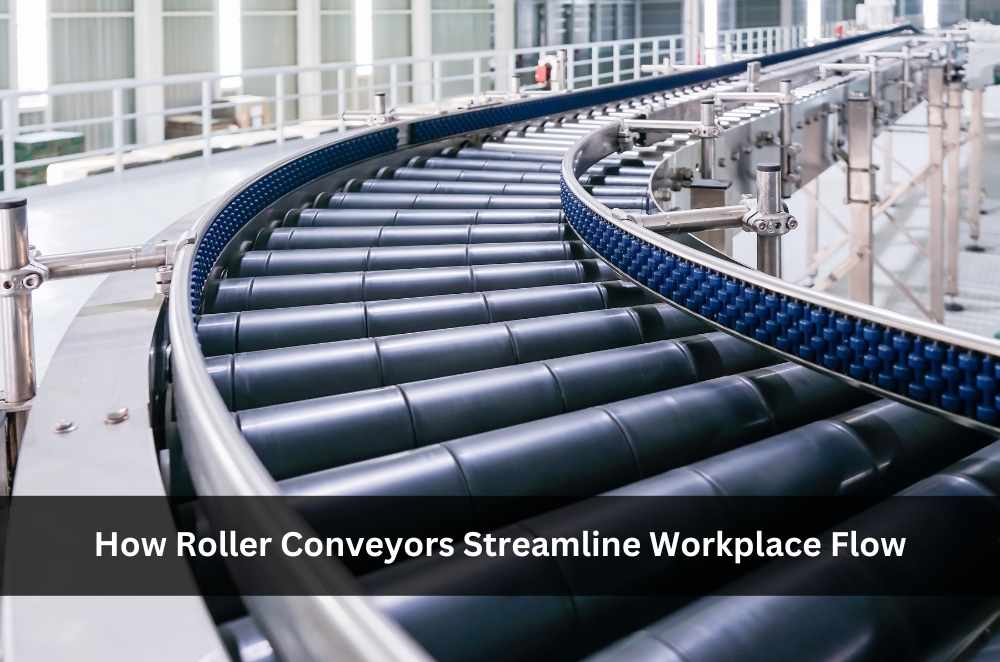
Smart facilities rely on gravity roller systems to move faster
A few years ago, I worked in a mid-sized warehouse where half our time was wasted moving cartons manually — from unloading docks to packaging benches, and then to dispatch. We didn’t think much of it until a consultant pointed out something obvious: we were spending more labour on moving items than on packing them.
Their suggestion? Install a few rows of gravity roller systems. No motors, no wiring — just smart layout, sloped rollers, and momentum. It was the cheapest change we made that delivered the biggest results.
Whether you manage a logistics centre, a manufacturing floor, or even a retail backroom, roller conveyors can dramatically streamline movement and reduce fatigue. Let’s break down how they work, why they matter, and where they make the most impact.
What is a roller conveyor?
A roller conveyor is a material handling solution that uses a series of cylindrical rollers to transport goods. Items move either by manual push (gravity-driven) or powered mechanisms like belts or chains.
There are two main types:
Gravity roller conveyors: Rely on a slope or manual force. Great for lighter goods and simple setups.
Powered roller conveyors: Use electric motors to move items automatically. Suited for larger or automated operations.
In this guide, we’re focusing on gravity roller systems, which are:
Low-cost
Easy to install
Require zero electricity
Versatile for most flat-bottom loads
Why roller conveyors improve workflow
1. Reduce manual handling time
Instead of lifting or carrying boxes across work zones, operators simply slide them down a roller line. This dramatically reduces:
Walk time
Repetitive strain
Unnecessary lifting
2. Improve task separation
Roller conveyors allow you to define stages of work:
Inbound inspection
Sorting
Packing
Shipping
With each zone physically separated, teams become more focused, and bottlenecks are easier to identify.
3. Increase throughput
Products move continuously, not in fits and starts. This speeds up everything from unpacking to palletising.
When we added rollers between our packaging benches and the dispatch bay, we shaved 18 minutes per pallet. Over a month? That was an entire day saved.
Where to use gravity rollers
The beauty of gravity rollers is their flexibility. They’re ideal for:
Warehouses and distribution centres
Packaging stations
E-commerce fulfilment rooms
Food and beverage production
Recycling or returns areas
Retail storerooms
And they’re not just for industrial spaces. I’ve seen them used in:
Airport luggage zones
Event bump-in/bump-out setups
Pop-up warehouse sales
If you handle physical items regularly, roller conveyors make the movement part easier.
What to consider when planning your layout
1. Floor space and workflow direction
Conveyors should follow your natural product flow. Don’t be afraid to create curves or dead-end zones for sorting.
2. Roller size and spacing
Lighter goods? Use smaller diameter rollers, spaced closely. Heavy cartons? Opt for larger rollers, wider apart.
3. Safety and ergonomic clearance
Leave enough space for walking lanes, handrails, and emergency exits. Ensure staff don’t have to bend or twist repeatedly.
4. Load type and base
Rollers are best for flat-bottom items. For irregular shapes, use trays or pallets.
For help comparing options, check out our guide on how to choose the right conveyor for your space.
Real-world example: a fulfilment centre success story
We had a fulfilment client processing 600–900 parcels a day with a team of seven. Before they introduced conveyors, workers had to pass boxes down a line manually.
After installing just two 6-metre gravity conveyor lanes:
Throughput increased by 21%
Shoulder and wrist fatigue complaints dropped
Breakage rate on fragile goods declined
They reduced staffing from 7 to 5 per shift, reallocating the others to QA
They didn’t automate — they just optimised the flow. Sometimes simplicity wins.
Addressing manual handling risks
One of the biggest causes of injury in warehouses and workspaces isn’t equipment failure — it’s human strain. According to Safe Work Australia, tasks involving lifting, pushing, or pulling are a major contributor to workplace musculoskeletal injuries.
Using roller conveyors directly supports safer workflows by:
Reducing the need to carry heavy items manually
Encouraging neutral movement patterns (no awkward twisting or bending)
Minimising repetitive strain during unloading or sorting
You can read more about these risks and how to reduce them in the official manual handling guide from Safe Work Australia.
If you’re building a case for workflow upgrades in your organisation, this is a helpful document to include.
Maintenance and upkeep tips
One reason gravity conveyors remain popular? They’re nearly maintenance-free.
Still, here’s what I recommend:
Weekly wipe-down of rollers
Monthly check for jammed bearings
Quarterly inspection of frame alignment and floor bolts
Replace any damaged rollers immediately — they can cause jams or uneven flow
Avoid using harsh solvents on PVC rollers — use a damp cloth or mild cleaner. If your goods involve liquids or food, consider stainless-steel rollers for easier cleaning.
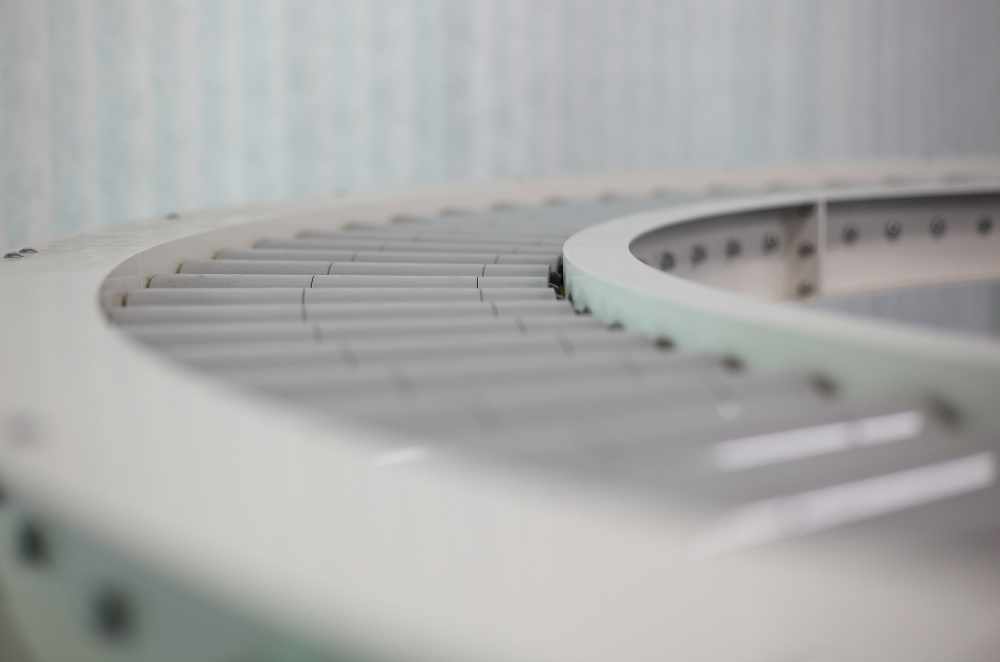
Sustainability and ROI benefits
Conveyors aren’t just efficient — they’re green.
How they help:
No power usage = low environmental impact
Fewer forklifts = lower emissions and noise
Reduces damaged goods = less waste
Lasts years with proper care
Compared to powered systems, gravity rollers have a payback period of weeks, not years. One project we advised paid off the investment in just 6 weeks through time saved alone.
Common misconceptions (busted)
“Roller conveyors are noisy.”
Not if you buy quality rollers with sealed bearings.
“They’re hard to install.”
Most gravity conveyors come modular — no tools needed beyond a spanner.
“You need a big space.”
You can get compact versions starting from 1.2 metres — perfect for benchtop use or tight backrooms.
Frequently asked questions
Q: What’s the weight limit for gravity conveyors?
A: It depends on the roller material and the frame. Standard models handle 50–100 kg per metre.
Q: Can you curve gravity conveyors?
A: Yes. Curved roller sections are available and often used to redirect flow without needing motors.
Q: Can I move them around?
A: Many come with lockable casters for mobile setups. Great for seasonal layouts or pop-up stations.
Final thoughts
When it comes to smart material handling, roller conveyors are the unsung heroes. No wires, no power, no headaches — just better workflow, reduced strain, and faster throughput.
Whether you're managing a warehouse, a production room, or a busy retail floor, gravity roller systems offer a cost-effective, scalable way to optimise your operation.
And if you’re still exploring their role in distribution settings, check out this deep dive on the benefits of roller conveyors in warehouses.
Write a comment ...