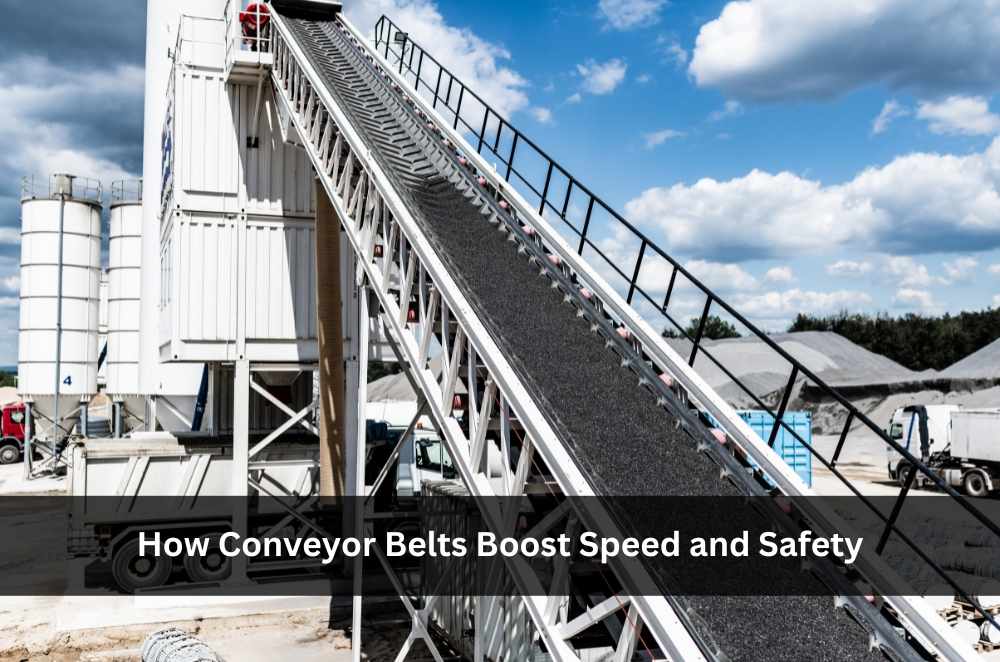
Why conveyor belts are more than just a moving surface
For many Aussie businesses — from warehouses to worksites — conveyor belts might seem like a behind-the-scenes utility. But the truth is, they’re one of the hardest-working systems on the floor.
A well-installed belt conveyor setup isn’t just about transport. It’s a force multiplier — slashing lead times, reducing injuries, and keeping workflow smooth in the most demanding environments.
I’ve worked with operators who underestimated their impact, only to realise post-installation that they could move double the volume, with fewer delays, and with fewer sore backs on the team.
So if you’re still moving products with forklifts, pallet jacks, or pure muscle power, it might be time to reconsider.
Conveyor belts make speed consistent, not chaotic
Let’s start with the obvious: speed. You can have the best crew in the world, but manual handling comes with natural limitations — people need breaks, get distracted, or simply move at different paces.
Conveyor belts eliminate that variability.
Whether you're shifting cartons across a warehouse or materials between workstations, conveyors provide:
Predictable timing — no delays between one item and the next
Uninterrupted flow — fewer bottlenecks and less downtime
Faster cycle times — jobs finish quicker without stop-start movement
Less waiting — downstream teams receive items right when they need them
I remember working with a Sydney-based fulfilment centre that was expanding fast. They introduced a low-speed powered conveyor belt between the pick and pack zones. Almost instantly, their order prep jumped by 28% — not because people worked harder, but because the flow didn’t stop.
Safety improves when lifting and pushing disappear
Speed’s great — but safety? That’s where conveyor belts quietly do their best work.
Manual tasks like lifting, carrying, and pushing are still some of the biggest causes of injury in Australian workplaces. From soft tissue strains to long-term wear and tear, they chip away at teams and budgets alike.
That’s why reducing those tasks through automation matters.
Safe Work Australia provides clear guidelines on hazardous manual tasks and how equipment like conveyors reduces physical demand. Their recommendations around machine guarding regulations and workflow design directly support conveyor adoption.
Here’s what a conveyor can prevent:
Workers twisting or straining to pick up boxes
Repeated bending to load/unload trolleys
Trips and slips from carrying oversized items
Fatigue from pushing heavy loads between zones
I’ve seen it myself — the difference in crew morale after removing just one repetitive task can be massive. No more “this job wrecks my shoulders” complaints. Just smooth movement, and less risk.
The right belt for the right job makes all the difference
Not all conveyor belts are created equal. If you pick the wrong type for your load or environment, you’ll end up with jams, spillage, breakdowns, or worse, injuries.
Let’s run through the most common conveyor belt types:
Flat belt – Ideal for light materials, parcels, and general goods
Modular belt – Great for food handling or liquids; allows airflow and drainage
Cleated belt – Best for inclined runs or loose bulk materials like sand or grains
Roller bed – For heavy items where friction reduction is key
Magnetic belt – Specialised for metallic scrap and recycling lines
Wire mesh – Useful in high-heat or wet washdown zones
Need more guidance? Here’s a detailed breakdown of the most common belt conveyors in use today.
The key is matching your belt to your product, not the other way around.
Speed doesn’t mean more maintenance (if you plan well)
One common fear with automated systems? That they’ll become high-maintenance headaches.
In reality, most conveyor belts are incredibly low-maintenance when installed correctly. Basic upkeep and inspection go a long way toward keeping them running smoothly for years.
Here are some quick-fire conveyor belt maintenance tips you can build into your routine:
Check belt tension weekly — overtight belts wear faster
Keep the system clean — debris causes misalignment
Lubricate rollers and chains as per the manufacturer's specifications
Inspect for belt wear and replace before damage spreads
Test emergency stops monthly — non-negotiable
At a facility I consulted for in Western Sydney, just 10 minutes of weekly maintenance prevented over $2,000 in downtime in a single quarter. It’s one of those things you don’t notice until you skip it.
Real-world success: one upgrade, many wins
In a recent fit-out for a medium-sized food packaging business, we replaced a mix of manual carts and roller tracks with two motorised belt conveyors.
The outcome?
38% faster line processing
70% drop in near-miss incidents (particularly slips near cold zones)
Reduced team fatigue by 40% (as reported in internal surveys)
Positive ROI achieved in under 5 months
One of the line managers said it best:
“It’s not just faster — it’s calmer. People aren’t rushing or cutting corners anymore.”
And when you scale that kind of impact across multiple departments or sites? That’s where your edge comes from.
Belt conveyors also future-proof your workflow
What I love about belt conveyors is their flexibility. You don’t need a 50-metre megasystem to get value. Even a short, three-metre conveyor between two key areas can change the tempo of a team.
Plus, they grow with you. Most modern setups are modular, meaning you can:
Extend a belt as your operation grows
Add inclines, diverters, or gates later
Integrate weighing, sorting, or scanning tools
Switch out belt types as your product range changes
Planning a facility upgrade? Take a look at some choosing the right conveyor system resources for layout, budgeting, and integration ideas.
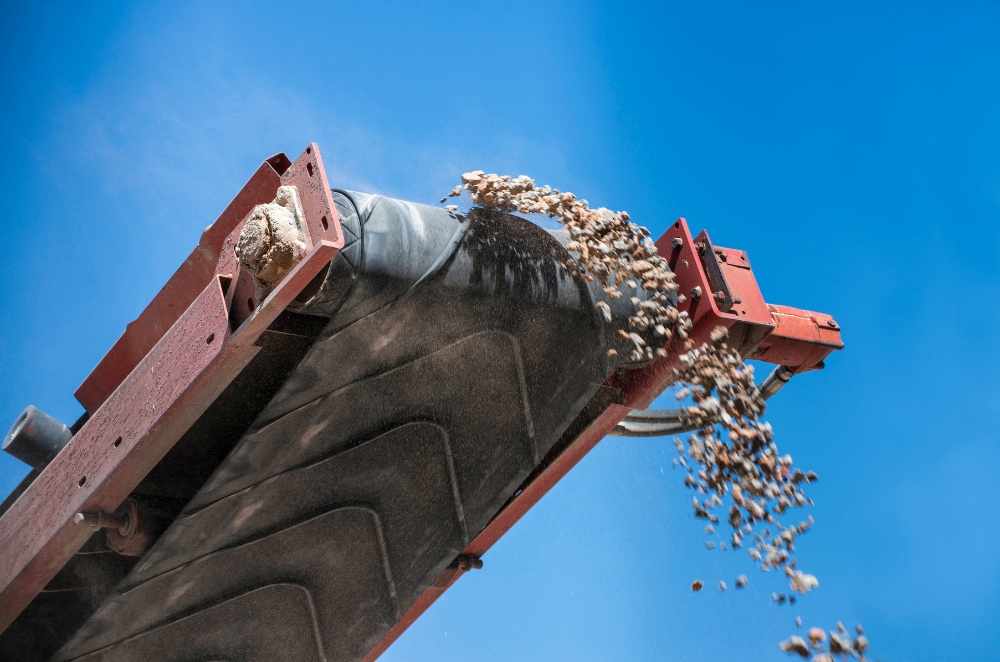
Still relying on manual movement? It might be costing you more than you think
If you're on the fence, consider this: every manual move costs time. Every strain risks injury. Every delay eats margin.
It’s not about replacing people — it’s about making their jobs safer and more efficient.
Belt conveyors deliver on both fronts:
They keep the product moving
They reduce repetitive strain
They support scaling up without scaling risk
Final thoughts
In today’s high-demand, low-margin world, conveyor belts do more than carry boxes — they carry your workflow, your safety record, and your bottom line.
And when you opt for professionally designed, modular belt conveyors, the gains aren’t just felt on the line. They’re seen in your reports, your uptime, and your crew’s well-being.
So whether you’re running a growing warehouse or modernising a site, a smarter conveyor setup isn’t just nice to have — it’s essential.
Write a comment ...