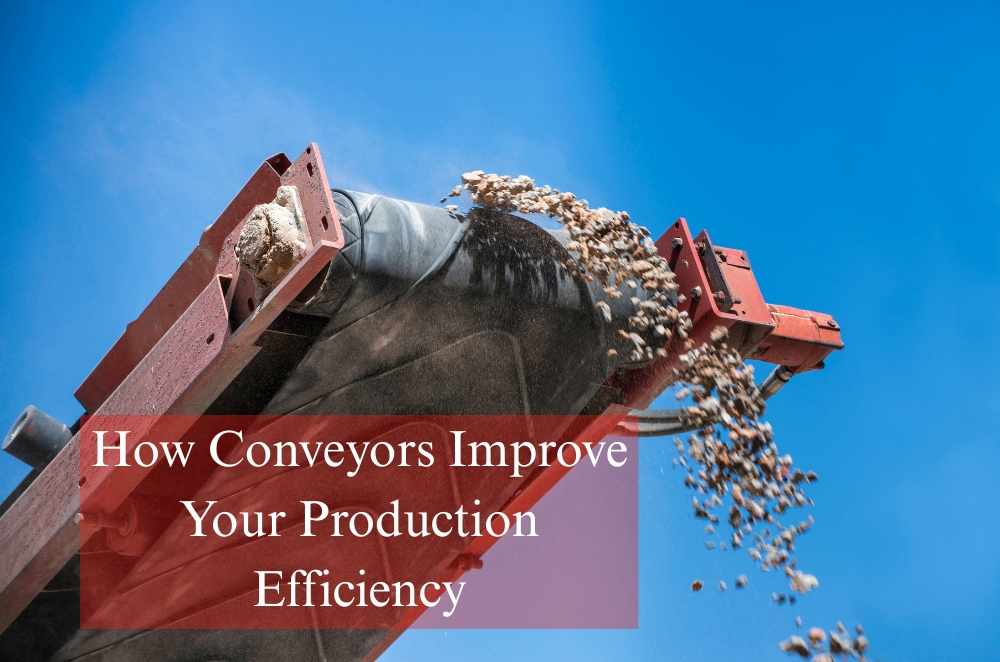
If you’ve ever spent time in a factory or warehouse, you’ve probably noticed how much smoother everything moves when conveyors are part of the picture. I remember walking through a distribution centre years ago and being struck by the steady rhythm—products sliding past in neat lines while people focused on checking quality and planning the next steps. It’s easy to underestimate how much conveyors can change the daily flow. Beyond saving time, they help reduce mistakes, support safer working conditions, and make it easier to keep up when demand picks up. A good system does more than shift boxes; it becomes the backbone of your production.
Cutting down on manual handling and fatigue
One of the first things businesses notice when they bring in conveyors is how quickly the load on staff eases up. All that bending, lifting, and carrying wears people out by the end of the day. When the heavy moving is automated, there’s more energy left for higher-skill tasks.
Less repetitive strain on shoulders and backs
Steadier output without workers getting worn down
Fewer hold-ups caused by fatigue
I’ve seen teams that used to spend hours shuffling pallets now standing comfortably at inspection stations. Over time, that shift in focus doesn’t just improve morale—it lifts productivity in ways you can measure.
Creating a safer environment across the floor
While conveyors move materials along, they also help avoid awkward lifting and the hazards that come with it. But it’s not a magic fix. Like any equipment, they need proper planning and upkeep to work safely.
Guarding and stop buttons to manage emergencies
Clear training so everyone knows safe procedures
Regular checks to spot worn parts or problems
It makes sense to look into the manual handling safety in Australia. They spell out practical steps to balance efficiency and worker wellbeing. Even simple improvements can prevent injuries and downtime later on.
Smoothing out the flow of production
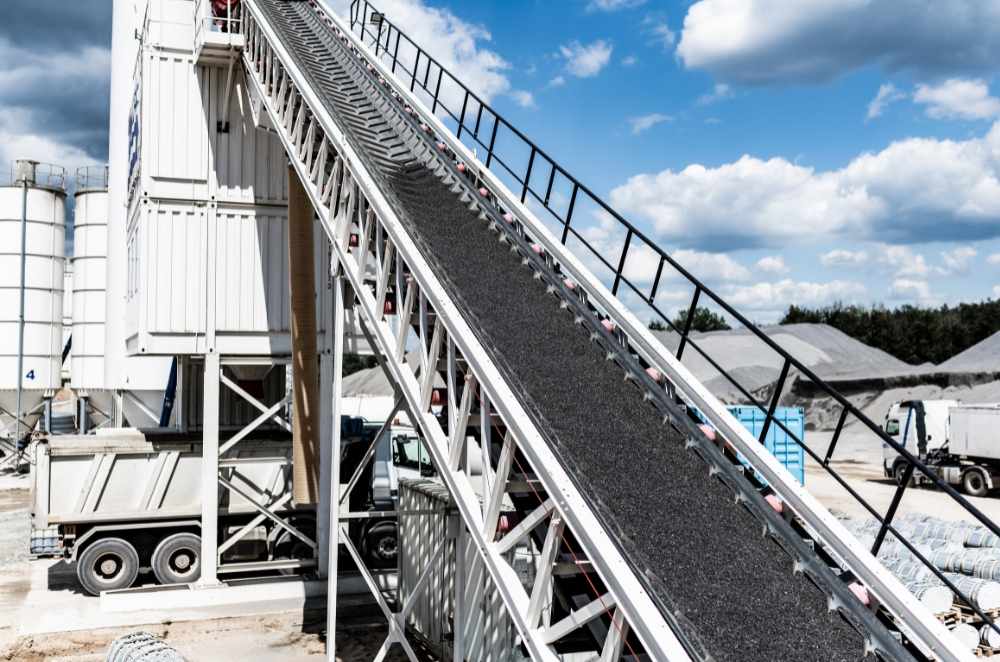
When materials rely on people to move them, you end up with small delays and inconsistent pacing. Someone’s taking a break, someone else is helping a colleague—it all adds up. A conveyor system keeps things rolling at the same tempo.
Deliveries reach the next station without delay
Planning becomes more reliable
Bottlenecks are easier to spot and fix
I once helped a manufacturer of household products who struggled with unpredictable output. Once they installed conveyors, they were finally able to plan shifts confidently, knowing each area would get what it needed on time.
Speeding things up without losing sight of safety
People often focus on speed first, and fair enough, faster production matters. But it’s worth remembering that smart conveyor design balances efficiency with protection. You don’t want a system that moves so fast it creates new hazards.
Variable speeds to suit different loads
Sensors that stop the line if something goes wrong
Quiet operation to cut down on noise fatigue
A mate of mine in logistics shared how they cut loading times nearly in half by adding automated sensors and controls. They didn’t just get more done—they also saw fewer incidents and less strain on staff. Stories about conveyor belt speed and safety show how much thought goes into balancing those priorities.
Allowing your business to scale up more easily
When demand grows, manual handling is often the first area to buckle. There’s only so fast you can load boxes by hand. Conveyor systems give you room to expand without immediately hiring more people or redesigning the whole workflow.
Modular designs that can be extended
New sections added with minimal disruption
More predictable throughput when volumes rise
I remember visiting a mid-sized packaging company that had started with a single conveyor and expanded to a whole network over a few years. It lets them handle triple the volume without moving to a bigger facility.
Reducing mistakes and keeping products in good shape
Human error happens, especially when people are tired or rushed. One person packs carefully, another tosses items on top of each other. With conveyors, you get a steady pace and a predictable process.
Even spacing between products avoids collisions
Checks built into the line catch errors early
Clear paths reduce the chance of items getting mixed up
This is especially important for fragile or regulated goods. I’ve seen electronics assembly lines where a single slip could ruin high-value stock. Conveyors reduce those risks simply by keeping movement consistent.
Making material handling more efficient overall
There’s a lot of hidden effort in moving things from point A to B. Lift here, record there, set it down, pick it up again. Conveyors blend those steps into one smooth movement.
Fewer touchpoints mean less time wasted
Workers can focus on monitoring and adjusting
Training becomes simpler with less manual labour involved
I’ve read case studies about the conveyor advantage in operations, and it’s striking how much time is saved. It’s not about replacing people—it’s about freeing them to work smarter.
Designing a system that fits your space
Not every building is a clean rectangle. You’ll find awkward corners, tight aisles, and machinery you can’t just move. Modern conveyors adapt to all kinds of layouts.
Curved designs to get around corners
Custom heights for ergonomic loading
Specialised belts for different materials
I worked with a site that had a U-shaped production floor. Installing conveyors with adjustable speeds meant they could keep materials flowing without knocking down walls or changing the overall footprint.
Final thoughts on how conveyors change operations
There’s a reason conveyors show up in so many industries. They help you work faster, with less strain and fewer mistakes. Over time, those small daily gains build into something bigger—more orders filled, better quality, happier staff. I’ve seen operations that looked chaotic get transformed by automating what used to be tedious manual steps. Of course, it takes planning, training, and the right equipment to get it right. But when you invest in a conveyor system that fits your goals, you’re investing in smoother days and a stronger business. It’s not just about moving things faster. It’s about making the whole process more dependable, so you can keep growing with confidence.
Write a comment ...